The Material Planner Overview
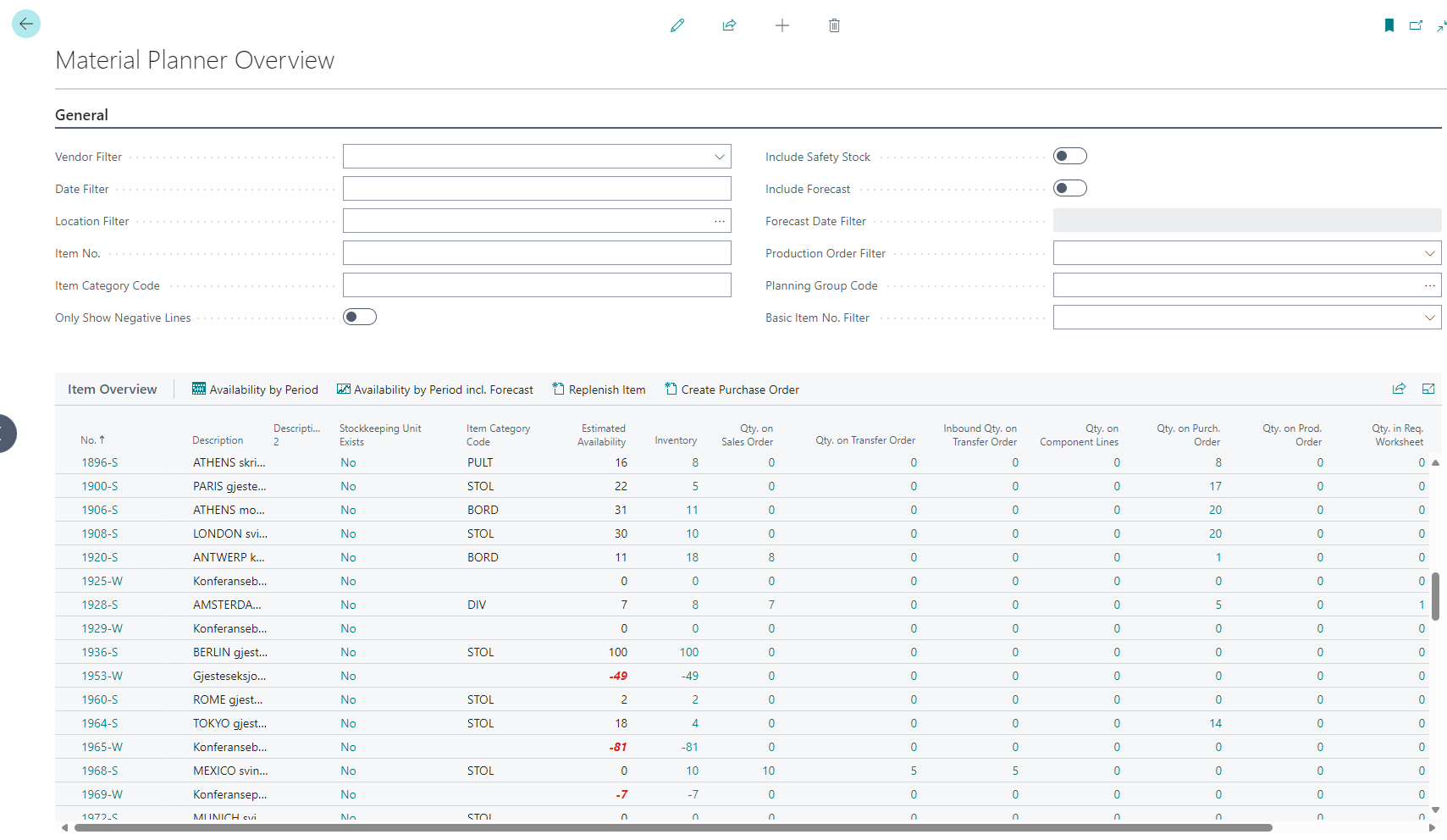
The Material Planner Overview gives a fast and simple overview of the estimated availability of your items. You can also see all the factors that make up the estimated availability such as how much of an item is being sold, purchased, or produced.
The program allows you to combine various filters to investigate specific items and identify those that require replenishment. You also have the option to directly create purchase requisitions/orders and production orders for these items in the program.
You can also export your data to Excel by clicking on the icon in the top right corner of the list.
Following is a description of the actions and fields displayed on the page.
General Fields

To get an overview of only relevant items, the Material Planner offers several built-in filters that can be combined as needed.
Vendor filter
Select item based on their supplier.
Date Filter
Choose the time period for calculating availability. Information outside the specified period will not be included in the calculation.
Location Filter
Choose the locations you want to examine. Use “|” between locations to see multiple locations, or “<>” to exclude certain locations. If this filter is empty, availability is calculated for all locations.
This field can be set to a default value that will be set every time you open the page. See the field Default Location Filter in the Material Planner Setup.
Search for specific items via item number.
Item Category Code.
Search for specific item categories via category number.
Only Show Negative Lines
By activating this filter, only items with a Projected availability of less than 0 will be displayed. This makes it easy to isolate items that require replenishment.
Include Safety Stock
By activating this filter, safety stock is included in the availability calculation. The value set as safety stock will be subtracted from the Projected availability.
This field can be set to a default value that will be set every time you open the page. See the field Include Safety Stock by Default in the Material Planner Setup.
Include Forecast
Adds the forecast for the items in the calculations. Especially relevant for items with longer lead times to get an overview of future needs.
This field can be set to a default value that will be set every time you open the page. See the field Include Forecast by Default in the Material Planner Setup.
Forecast Date Filter
Specify the time period to include in the forecast calculations. Select how far into the future you want to see, and exclude older forecast entries that are no longer relevant.
This filter can only be used when Include Forecast is selected.
Production Order Filter
Search for specific production orders to get an overview of items relevant to these.
Planning Group Code
Search for planning groups. Groups you create that contain components/items used in the production of other products. This makes it easier to see if you have all the needed components for your products.
Base Item Filter
Search for specific base items
Actions

Availability by Period
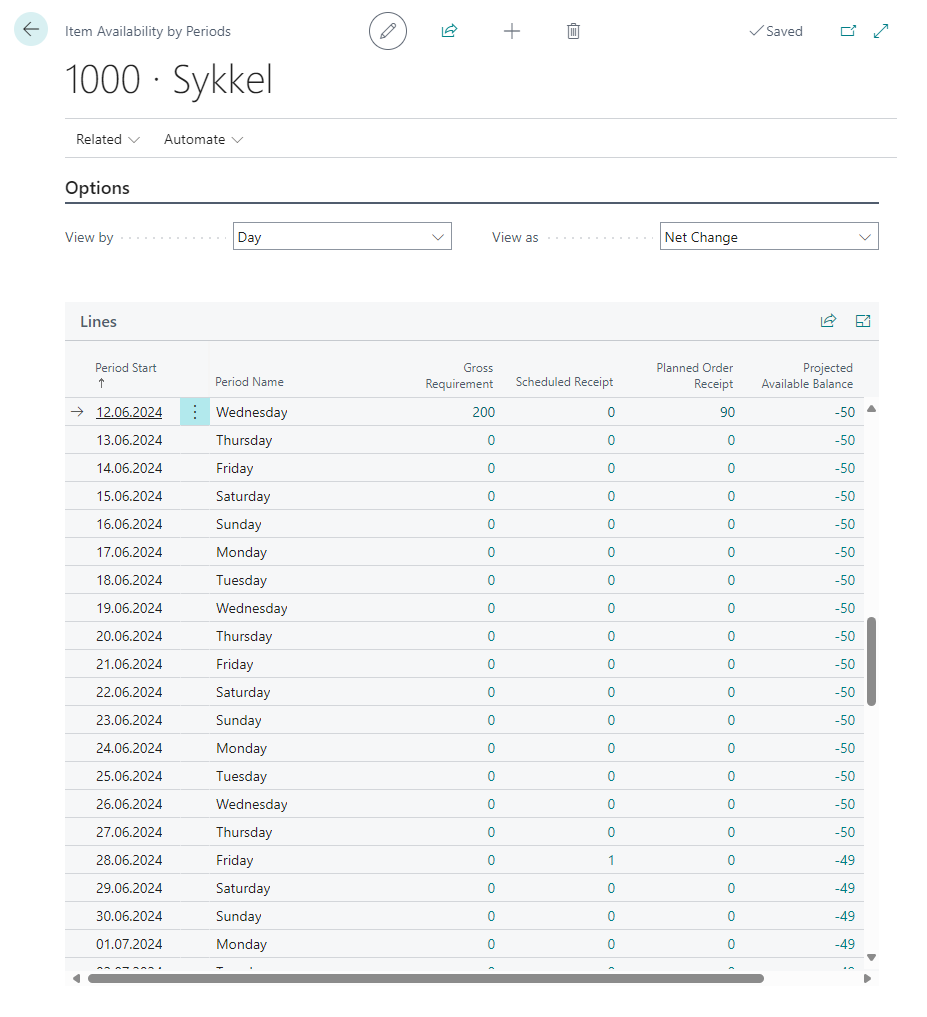
This action opens a page that shows the projected quantity of the selected item over a chosen period (day / week / month / quarter / year / accounting period). This provides a clear overview of the inventory and makes it easy to identify periods when the items require replenishment.
Availability by Period with Forecast Included
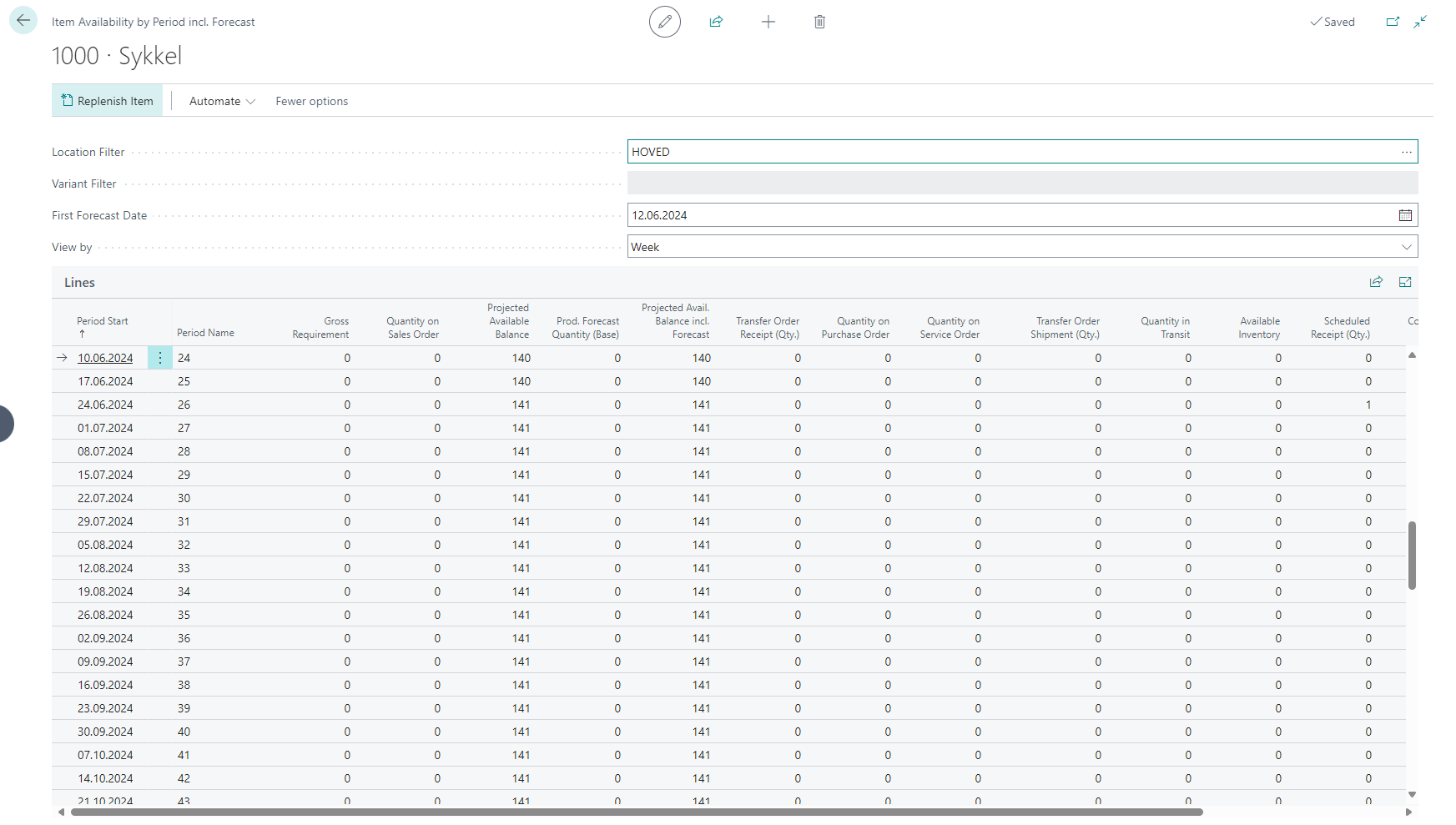
By including the forecast, the program will add a column for Projected available balance incl. Forecast that takes forecast data into account. You will also have the option of filtering by different warehouses and specifying forecast dates relevant to the calculation. This gives you a better overview and allows you to plan replenishment for items in advance.
For more information see Availability by Period with Forecast Included.
Item Replenishment
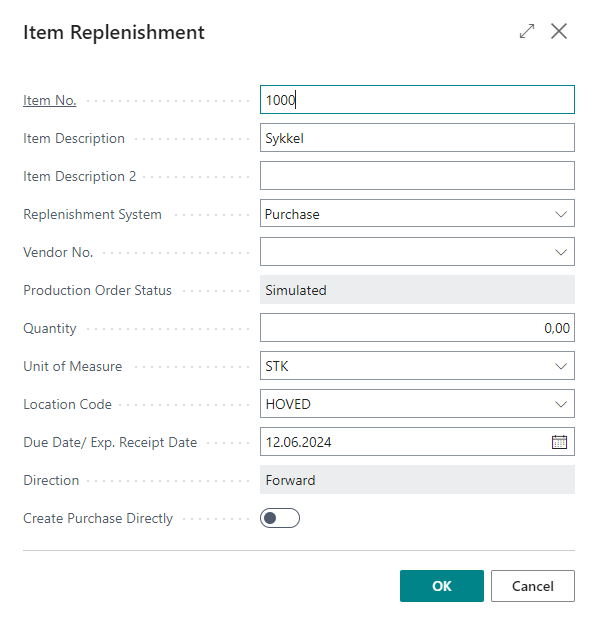
This action opens a window that allows you to create purchase requisition/order or production order for the selected item. The choice of the Replenishment system field determines whether the order is set to purchasing or production. Many of the values will already be filled in based on the item card, but can be overridden before the order is created. This way you can easily place orders for items that require follow-up.
For more information see Item Replenishment.
Create Purchase Order
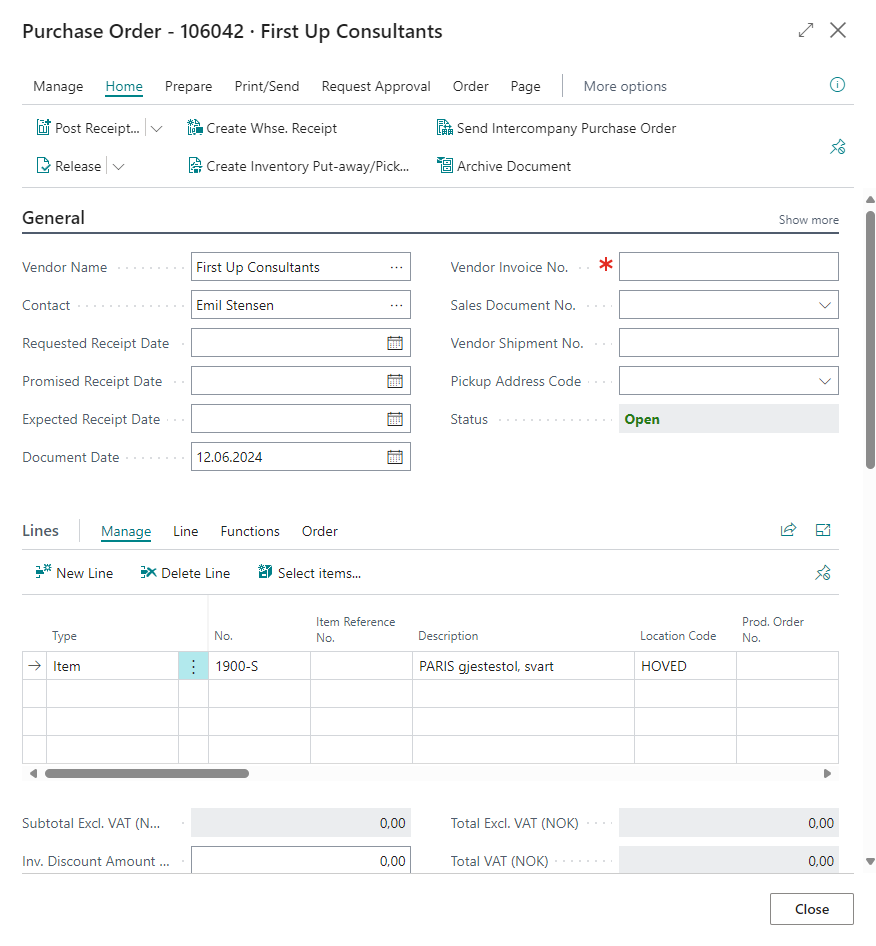
To use this action the Vendor Filter has to be set to the vendor you want to order from. Then you can easily place an order for multiple items from the same vendor in a single step. This can save a lot of time and simplify the ordering process for both you and the vendor.
For more information see Creating Purchase Order.
Fields on the Item Overview

No.
The Item Number of the Item being analyzed.
Description
The Item's Description.
Description 2
The Item's Description 2.
Stockkeeping Unit Exists
Yes/No indicating if there is an inventory unit for the item. For more information see Stockkeeping Unit.
Item Category Code
The Item Category Code to which the Item belongs if any. The value is retrieved from the item card.
Estimated Availability
In this field, the Material Planner calculates the value based on the following factors:
Inventory
Quantity in Production Orders
Quantity on Order
Quantity in Purchase Orders
Quantity in Transfer Orders (To Location Code)
Quantity in Transfer Orders (From Location Code)
Quantity in Sales Orders
Quantity on Production Order Components
Quantity in Forecast (if the field is activated)
Safety Stock Quantity (if the field is activated)
If this value is less than 0 you do not have a sufficient quantity of items to fill your orders.
Inventory
Amount of the item currently in stock.
Qty. on Sales Order
Indicates the quantity in Sales Orders.
Qty. on Transfer Order
Indicates the quantity of the item on Transfer Orders being sent from your warehouse.
Inbound Qty. on Transfer Order
Indicates the quantity of the item on Transfer Orders being received at your warehouse.
Qty. on Component Lines
Indicates the quantity of the item which is planned for production of other items/products.
Qty. on Purch. Order
Indicates the quantity of the item on Purchase Orders.
Qty. on Production Order
How much of the Item you have on Production Orders.
Qty. in Req. Worksheet
Indicates the quantity of the item on Requisition Lines.
Vendor No.
Displays the item’s default vendor. The value is retrieved from the item card.
Maximum inventory
Indicates the maximum level of inventory for the item. The value is retrieved from the item card.
Safety Stock Quantity (Only visible if Safety Stock is included)
How much of the Item is reserved as Safety Stock. The value is retrieved from the item card.
Quantity in Forecast (Only visible if Forecast is included)
How much of the Item is on Demand Forecast Entries.